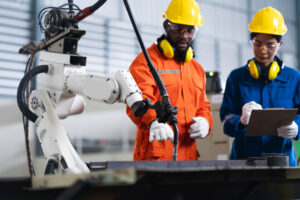
Fabricated Structural Steel Engineering, Mechanical, Electrical, Electronics Engineering and Information and Communications Technology Services
We provide seamless fabricated structural steel engineering design, repairs and prototype services that are guided by quality (ISO 9001) safety (ISO 45001) and technical product documentation to ISO 128. We optimize welding joint design, test and commission in line with ISO 3834, certified by all the personnel and bodies relevant for certification. Streamlined welding and structural design processes are amplified by non destructive testing (NDT) inline with ISO 17365. ISO compliance is the leading guide, supplemented with the local SANS standards where required.
Integrated solutions that are essential in modern engineering, particularly in areas like automation, smart systems, and IoT (Internet of Things). These multidisciplinary services are increasingly important in developing advanced systems that require seamless integration across different engineering domains.
Consulting and Professional Services
- Technical Documentation: Preparation of technical manuals, reports, or documentation for a product or process.
- Project Management: Providing project management services for a small to medium-sized project.
- Feasibility Studies: Conducting a feasibility study for a proposed engineering project.
Structural Steel Engineering Services
The design process for fabricated structural steel products is a highly coordinated effort involving multiple stages, each governed by industry standards and codes to ensure safety, functionality, and efficiency. Below is a step-by-step outline of the fabricated structural steel engineering process, including the relevant codes, typical timelines, and a discussion of cost factors at each stage.
Structural Steel Engineering Process:
1. Project Concept & Initial Planning
- Description: In this phase, the scope of the project is defined, and the design objectives are outlined, including load requirements, site conditions, and architectural preferences.
- Codes: The primary codes governing structural steel design are:
- AISC
- BS EN 1993
- Timeline: Typically 2-4 weeks for initial project planning and scope definition.
- Costs: Low (5-10% of the total design cost), covering meetings, consultations, and preliminary design.
2. Preliminary Design
- Description: Basic layout of structural elements such as beams, columns, and connections. Engineers create initial design sketches and computer models.
- Codes:
- Load and Resistance Factor Design (LRFD) or Allowable Strength Design (ASD) from AISC in the U.S.
- National building codes like IBC (International Building Code) or local seismic and wind loading standards.
- Timeline: 2-6 weeks depending on complexity.
- Costs: Medium (10-15% of design cost). Includes software costs (e.g., AutoCAD, STAAD.Pro, or Tekla Structures) for design simulations.
3. Structural Analysis & Final Design
- Description: Detailed analysis of structural loads, stresses, and material behavior under conditions such as wind, seismic activity, and thermal loads. Engineers optimize the design for weight, strength, and cost-effectiveness.
- Codes:
- AISC 360 (Steel Construction Manual)
- ANSI/AISC 341 (Seismic Provisions for Structural Steel Buildings)
- ASTM A992 (Standard Specification for Structural Steel Shapes)
- BS EN 1993-1-1 for Eurocode steel structures.
- Timeline: 4-12 weeks depending on the complexity of the project.
- Costs: High (20-30% of design cost). Structural analysis often requires expensive simulation tools and in-depth calculations. Consulting fees for structural engineers also contribute.
4. Detailing & Fabrication Drawings
- Description: Creation of detailed shop drawings for fabrication. These include dimensions, steel grades, welding specifications, and bolt locations. Detailing is critical to ensure that fabrication and installation proceed smoothly.
- Codes:
- AISC 303 (Code of Standard Practice for Steel Buildings and Bridges)
- AWS D1.1 (Structural Welding Code for Steel) for welding details.
- Timeline: 2-8 weeks depending on project scale.
- Costs: Medium to high (15-20% of total design cost). This stage often requires precise 3D modeling and collaboration between engineers and fabricators. Specialized software like Tekla, SolidWorks, or Revit is used.
5. Procurement of Steel Materials
- Description: Once drawings are approved, the raw steel is procured. Material specifications are based on the design, and quality testing ensures compliance with structural standards.
- Codes:
- ASTM standards, such as ASTM A36 for carbon structural steel or ASTM A572 for high-strength low-alloy structural steel.
- ISO 9001 (Quality management) or local quality standards for steel manufacturing.
- Timeline: 4-8 weeks (can vary based on market conditions and supplier availability).
- Costs: Material costs form a large portion of the project budget (40-60% of the total cost). Costs depend on market price fluctuations for steel and specific grades required for the project.
6. Fabrication
- Description: Steel is cut, shaped, welded, and assembled into components as per the fabrication drawings. Quality control measures include dimensional checks, weld inspections, and load testing.
- Codes:
- AISC 360 for construction tolerances.
- AWS D1.1 for welding.
- ISO 3834 for quality requirements in welding.
- Timeline: 6-12 weeks depending on project scale and complexity.
- Costs: Medium to high (20-30% of total cost). Labor costs, welding, and finishing processes like galvanizing or painting are significant contributors to the budget. CNC cutting and automation can reduce costs.
7. Inspection and Quality Control
- Description: Inspections are conducted at various stages of fabrication to ensure that steel components meet design specifications and quality standards. Non-destructive testing (NDT), such as ultrasonic or radiographic testing, may be conducted to detect flaws.
- Codes:
- AWS D1.1 (for welding inspection)
- ISO 17635 (NDT standards for metallic materials)
- Timeline: Conducted throughout the fabrication phase.
- Costs: Typically 5-10% of fabrication cost. Costs include inspection fees and possible rework due to non-conformance.
8. Transportation to Site
- Description: Once fabricated, steel components are transported to the construction site. Oversized loads or special handling may require specialized vehicles and permits.
- Codes:
- DOT (Department of Transportation) or local transportation regulations.
- OSHA guidelines for load handling safety.
- Timeline: 1-3 weeks, depending on location and complexity.
- Costs: 5-10% of project cost. This includes logistics, transportation permits, and potential storage at the site.
9. On-Site Assembly & Erection
- Description: Steel components are assembled and erected on-site using cranes, temporary supports, and precision equipment. Bolting, welding, and alignment are critical tasks during this phase.
- Codes:
- AISC 303 for erection tolerances.
- OSHA 1926 for safety in steel erection.
- Timeline: 4-12 weeks depending on project complexity and weather conditions.
- Costs: High (20-30% of total project cost). Labor costs, crane rentals, and on-site management contribute heavily to the budget.
10. Final Inspection and Handover
- Description: A final inspection is conducted to ensure all elements are installed correctly and meet project specifications. Any non-compliance is addressed before project handover.
- Codes: Building codes and local construction laws.
- Timeline: 1-2 weeks.
- Costs: Low (2-5% of project cost), mainly administrative and inspection-related expenses.
Mechanical Engineering
- Product Design Initial design and prototype development of a and Prototyping : mechanical component or system.
- Machinery Analysis: Conducting stress analysis or performance optimization for an existing machine or system.
Electrical Engineering
- Circuit Design: Design and development of custom electronic circuits for a specific application.
- Energy Audit: Performing an energy efficiency audit for a commercial or industrial facility.
Control Systems Design: Designing a basic control system for a small manufacturing or automation project.
Property Development
- Site Selection and Feasibility Analysis: Identifying and evaluating potential sites based on factors like location, zoning regulations, accessibility, and market demand. Conducting economic, environmental, and legal feasibility studies to assess the viability of a proposed development.
- Planning and Design: Architectural Design-Designing buildings and structures that meet the project’s aesthetic, functional, and regulatory requirements. Regulatory Approvals-Obtaining necessary approvals and permits from local planning authorities and regulatory bodies.
- Structural Analysis: A structural assessment or design for a residential or small commercial building.